Enhancing Reliability with Predictive Maintenance and Electric Motor Diagnostics
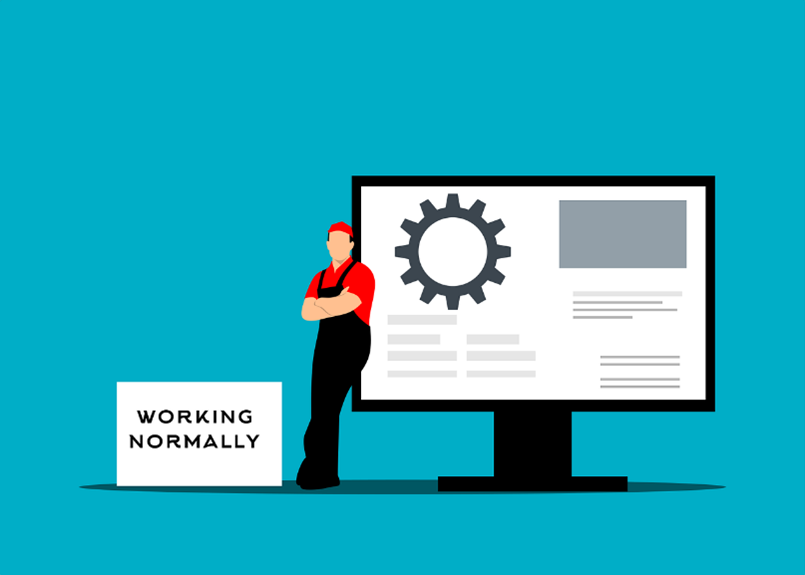
Predictive maintenance stands as a forward-thinking strategy that leverages data analysis to predict potential equipment failures. This method contrasts sharply with reactive maintenance, which deals with issues after they occur, and preventive maintenance, which follows a regular schedule regardless of need. By implementing predictive maintenance, issues can be addressed before they escalate, ensuring smoother operations, particularly valuable in industrial automation.
Implementing Predictive Maintenance
To adopt predictive maintenance, start by assessing your current procedures and identifying which equipment could most benefit. Gathering performance data is crucial in creating a strategy that incorporates appropriate technology and personnel. Learning from case studies of successful applications can guide the development of a maintenance plan tailored to specific needs.
Leveraging Sensor Data and Advanced Diagnostics
At the heart of predictive maintenance for electric motors is sensor data. Utilizing sensors, such as those for vibration and temperature, helps monitor motor conditions and predict potential failures. Advanced diagnostics tools like electrical motor current measurements, machine learning, and AI enhance the analysis of this data, spotting trends and anomalies that indicate impending issues, allowing for timely interventions.
Proactive Management of Motor Health
Proactively managing motor health is critical in minimizing disruptions in industrial automation. Real-time monitoring allows for the early detection of issues, enabling maintenance to be scheduled during planned downtimes rather than causing unexpected disruptions. Integrating predictive maintenance into existing systems ensures continuous operation and optimizes overall system performance.
Future Directions in Motor Maintenance
The outlook for predictive maintenance is promising with continual advancements in sensor technology, data analytics, and machine learning. Staying abreast of these developments can help maintain a competitive edge by enabling more precise and efficient maintenance strategies.
Predictive Maintenance Benefits Across Electrical Components:
- Motor Starters: Identifies wear and tear early, enhancing lifespan and operational continuity.
- Variable Frequency Drives (VFDs): Early detection of flaws improves operation, energy efficiency, and reduces the risk of failures.
- Combination Starters: Early diagnostics help avoid issues like overheating, ensuring reliable motor control.
- Motor Contactors: Monitoring detects wear, preventing malfunctions and maintaining dependable performance.
- PLCs (Programmable Logic Controllers): Continuous tracking ensures fault-free operation, preserving system reliability.
- Control Relays: Anticipates failures, facilitating timely maintenance to avoid interruptions.
- Motor Control Centers: Detects issues such as loose connections early, preventing significant operational disruptions.
Predictive maintenance based on motor diagnostics is an essential strategy for enhancing reliability in industrial automation. By understanding, implementing, and continuously advancing in predictive maintenance, facilities can minimize downtime and extend the lifespan of their machinery. Instead of waiting for failures to occur, proactive measures can prevent them, keeping operations running smoothly and efficiently.
We salvage and repair electrical products, including bus duct, bus plugs, and more! If you’re looking to buy or sell industrial electrical equipment, J&P Electrical is your answer!
J&P Electrical is a full-service electrical supply company. At J&P, we source contractors, end-users, and supply houses with new surplus, quality reconditioned, and obsolete electrical equipment. We also purchase a wide range of heavy industrial electrical equipment such as bus plugs, bus duct, transformers, circuit breakers, fuses, and switchboards. Call us at 877-844-5514 for assistance.
Written by the digital marketing team at Creative Programs & Systems: www.cpsmi.com